Hyperstripes meander patterns: Mechanical Simulation
Introduction
Patterns are used in the conductive tracks to create flexible electronics. The conductive materials, like Gold, Silver or Copper, typically are less strain-able than the substrate material they are placed on. The substrates (TPU’s) can take up to 100% strain easily, the conductors not (see figure #). Obviously, adding “length” to the conductive track would lead to an increase in resistance (and material use), and therefore undesirable in general. The pattern can therefore be designed as fit for purpose. To assess the strain-ability of the flexible conductors, Computer Design of Experiments (CDoE) were conducted. Finite Element Analysis models were made for HyPerStripes based on parametric models.
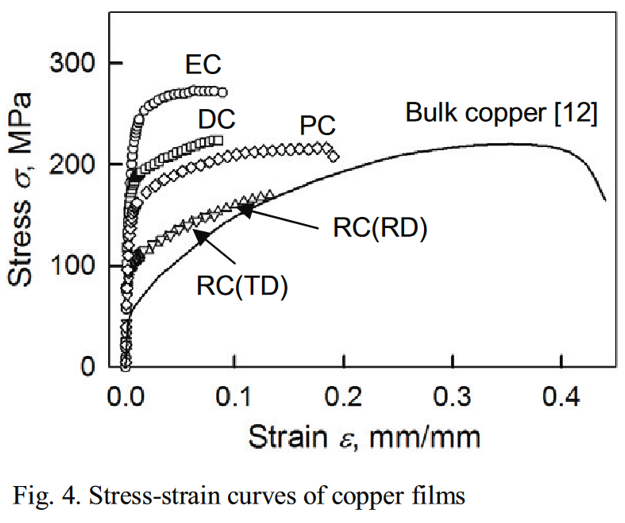
Zhang et al., Procedia Eng. (2011)
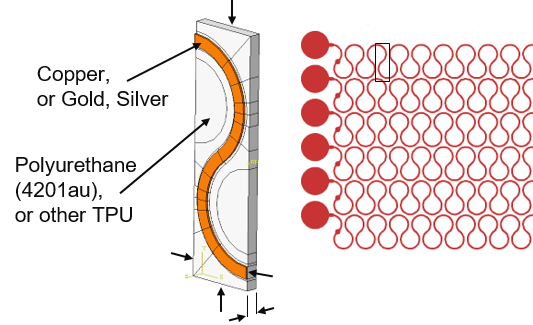
Wire thickness effects
The plastic strain results in the conductor are plotted as a function of the applied strain to the HyPerStripe (ΔL/L0)
- For the typical horseshoe design (shown below) we observe in the tensile test different responses depending on the wire thickness.
- The thickest wire results here in the most stretchable design.
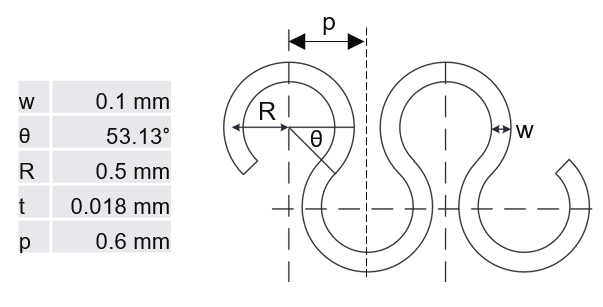
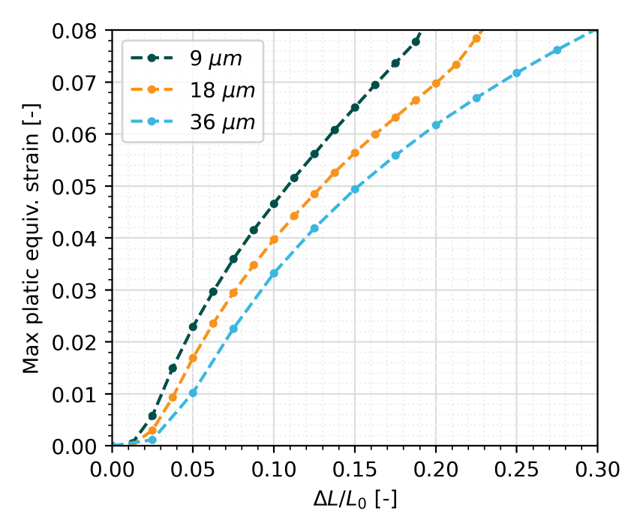
Wire width effects
- Varied wire width: w
- The thinner wires compared to the w = 0.1mm case show interestingly more stretchability initially.
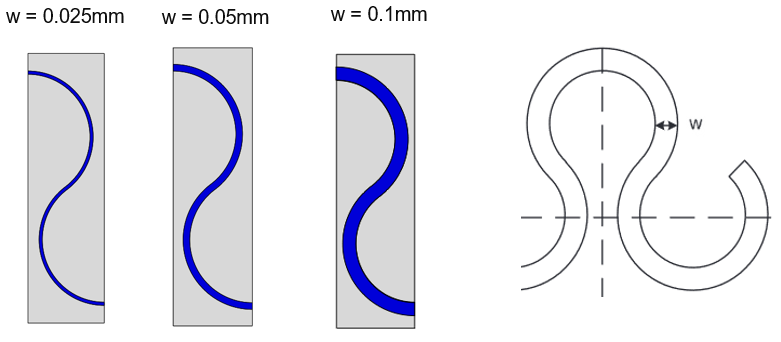
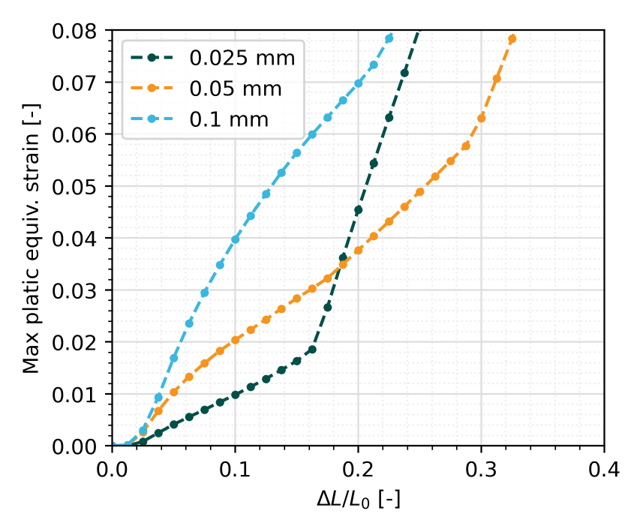
- The thickest wire develops plastic strain in the mid-section due to bending effects (1 & 2).
- Depending on the amount of stretch, the thinner wires develop for the large strain case, (2), mainly plastic equiv. strain around the tops.
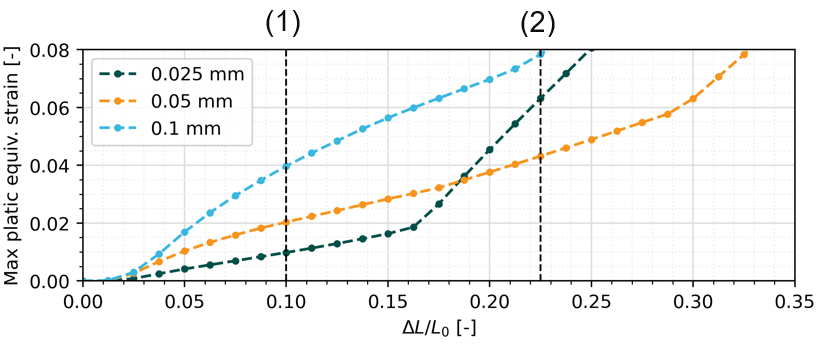
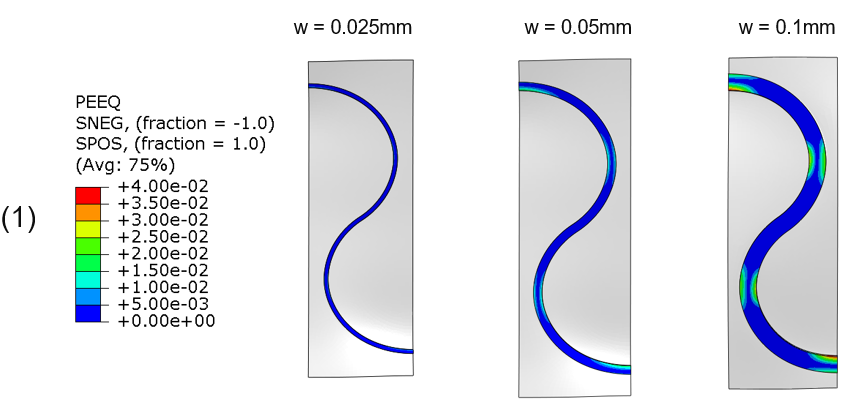
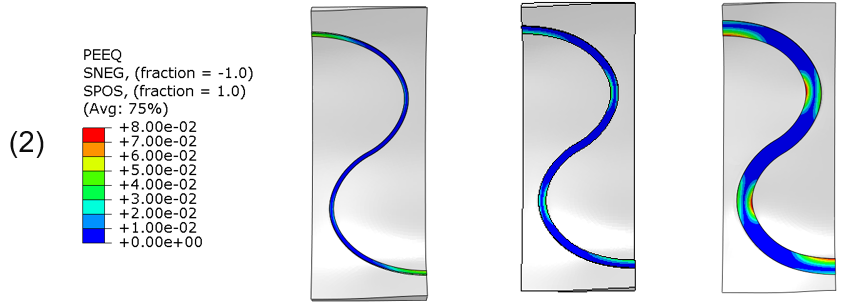
Design optimization
As a basis for the parametric models, tow possible design are evaluated, a horse-shoe like design and a block shaped design. The relatively straight-forward designs have up to 6 design parameters which were varied, keeping the polyurethane substrate material (4201AU by Covestro) and the conductor base material (Copper) constant. These materials can be replaced by others in the CDoE. From the mechanical point of view, the plastic strain in the conductive material was used as the critical parameter for assessing the “performance” of each design. The conductivity of the track was assumed to be unchanged up to the failure strain of the conductors.
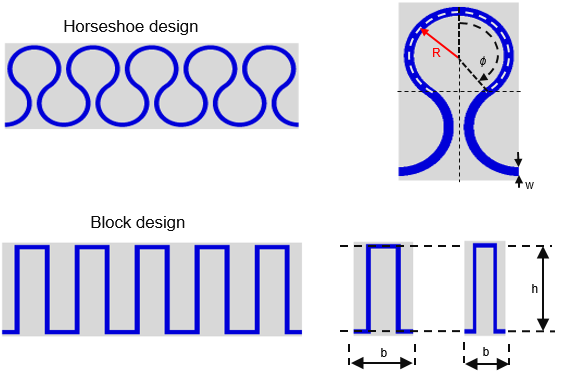
Design tool
For designing, the engineer would probably ask: “what is the design we need to fulfil the requirements”. To answer this question, the results of the CDoE are made available to Design Space Exploration (DSE) software. The results is that the engineer can define the requirements and gets the design back as a solution.
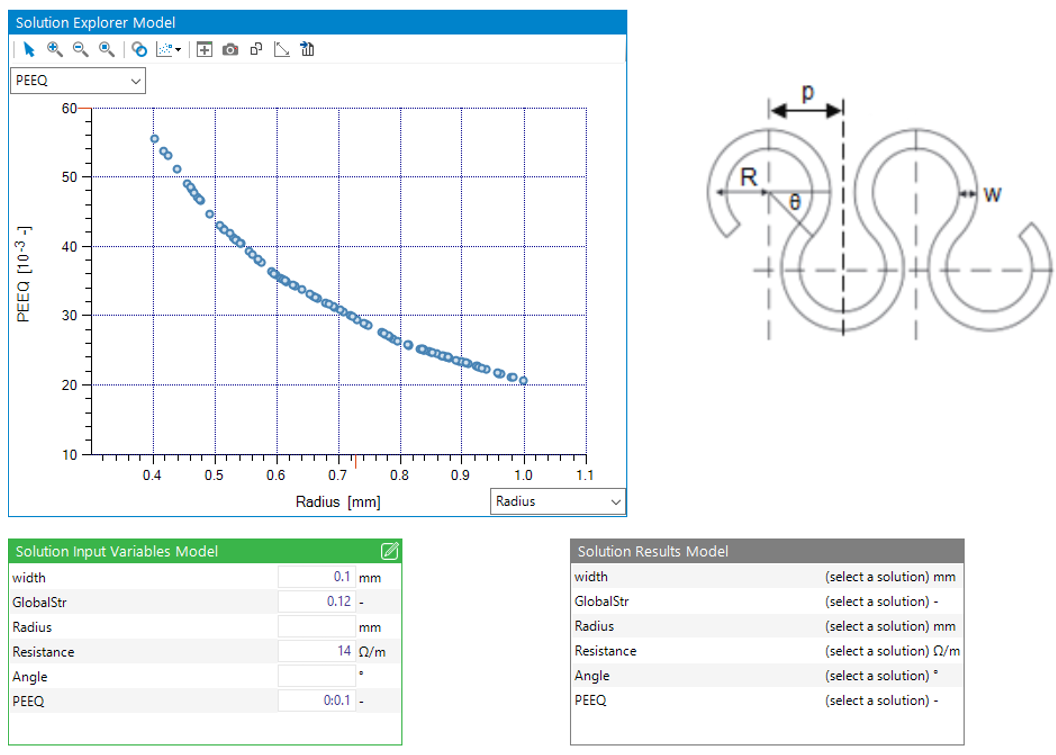
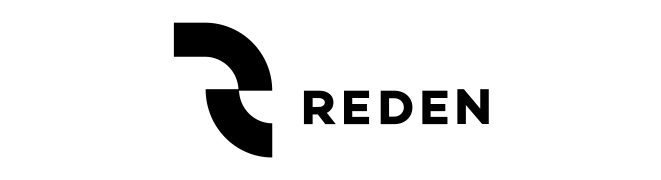